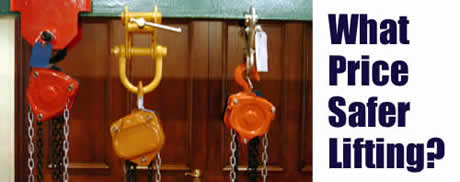
Beware the low cost option, says Lifting Equipment Engineers Association chief executive Derrick Bailes, the third in a series of features. |
Straightforward equipment failure is a relatively unusual factor in lifting accidents. But while effective staff training and proper planning of lifts are rightly being afforded greater emphasis, this should not be at the expense of the correct approach to the selection and maintenance of the equipment itself. Poorly designed, manufactured and maintained appliances are clearly a major risk to safe and efficient lifting operations.
At the same time, even the highest quality equipment can prove lethal if used inappropriately.
To meet acceptable standards of safety, what are the basic criteria that lifting equipment should meet? All should be of adequate strength, sound material of good construction and suitable for the duty that it has to perform.
Furthermore, appliances should have an adequate factor of safety incorporated into the design, allowing for wear, impact, dynamic loading and accidental overloading. Alongside these general principles, all lifting equipment should also have a 'birth certificate'. In the case of equipment placed on the European market, this will now come in the shape of the CE marking and declaration of conformity, indicating compliance with 'essential safety requirements'.
Given the fiercely competitive nature of modern industry, price is bound to play a significant role in the choice of lifting equipment. However, buyers who simply source the cheapest available product of a given specification lay themselves open to a number of risks. The growth of the 'global market' has certainly brought with it some extremely low cost equipment but also some very questionable quality standards. Unfortunately, a CE marking cannot in itself be taken as an absolute guarantee of acceptable safety and performance. Take, for example, the case of a brand new hand chain block recently seen on sale in the UK for less than £40 ($60): at this price level it is very difficult to see how quality standards have not been compromised beyond what could be considered reasonable for an overhead, load bearing appliance. Regardless of a CE marking, if extremely cheap equipment is implicated in an accident then a court is likely to ask if those responsible have really paid due care and attention to the health and safety implications.
Whatever the appliance in question, where lifting equipment is concerned the need to look beyond the price tag is paramount. The market has seen plenty of examples of counterfeit or grey market equipment in recent years and the purely price-driven buyer is the most vulnerable to equipment of dubious origin. Furthermore, once manufactured, certain types of lifting equipment can prove extremely difficult to inspect thoroughly. Perhaps the best advice that can be given is to seek out those suppliers that can demonstrate both a clear commitment to basic standards of quality and safety and the expertise necessary to guide buyers towards appropriate equipment. As far as this is concerned, it would be remiss not to point out that all potential members of Lifting Equipment Engineers Association (LEEA) are subject to rigorous audits before being accepted into the Association, and to further periodic inspections as long as they remain part of it.
Before lifting equipment is used, examination procedures may be necessary. Inevitably, legislation varies from country to country; in the UK, the relevant regulations are embraced by the Lifting Operations & Lifting Equipment Regulations (LOLER) and should, in theory at least, be reflected in domestic legislation across the EU. Under LOLER, through examination prior to use is not required if the lifting equipment has not been used before and has received a declaration of conformity no longer than 12 months before being put into service. However, a thorough examination is required if the safety of lifting equipment depends on the installation conditions. Regardless of specific legal obligations, the LEEA would endorse these guidelines as a sensible approach to the issue of verification prior to use.
In addition to a birth certificate and examination requirements, any equipment used for lifting operations should have a documented history of in-service inspection and maintenance. Again the relevant legislation will differ from one country to another but, in general terms, statutory requirements are increasingly offering the opportunity to employ a flexible, risk-based approach as an alternative to fixed maximum periods between inspections. This is usually a realistic alternative to fixed maximum periods between inspections. This is usually a realistic alternative alternative in three particular situations: where the condition of the equipment is dependent on the frequency and nature of its usage (assuming it can be monitored); where the condition of various parts of the machinery deteriorates at significantly different rates; or when equipment is appropriately stored and does not deteriorate significantly when not in use. However, although an examination scheme is usually more flexible and economic than a regime based on fixed maximum periods, the LEEA's experience is that relatively few companies have taken up this option, preferring to stock with the more traditional approach.
Once all the basic criteria have been met, attention inevitably shifts to selecting the most appropriate piece of equipment for a particular job. Lifting operations tend to fall into two basic categories; those that are done regularly and those that are done on a one-off or occasional basis. Notwithstanding what has already been said regarding the role of price, the nature of the application is bound to have an affect on what will be considered reasonable in terms of cost. A well-chosen appliance that is fully utilised and reduces the time taken to perform an operation can easily be justified in financial terms. For an infrequent lifting operation investment is much harder to support. However, while cost may be a factor in effectively deciding how quickly the lift will be performed, it must never be placed before safety.
Whatever the appliance in question, where lifting equipment is concerned the need to look beyond the price tag is paramount.
The first step in the decision making process is for the individual responsible to make an assessment of the operation. Issues to be addressed will include the weight, size, shape and nature of the load; clearly a grand piano is going to need a different type of sling from hot metal ingots - probably a man-made fibre webbing and chain sling respectively. Other factors to be considered will include the total height of the lift and whether the load needs to be lifted, jacked, pulled or moved through a particular plane. Is it indoors or outdoors? Is a suspension point available? Is a support structure required? How much workspace is available? Is there an electrical supply to hand?
Clearly no two lifts are the same, and it is impossible to highlight more than general issues involved in making the right choice of equipment. However, the most common errors include attempting to 'make up' lifting gear from what is around at the time. Slings and accessories come in a whole variety of designs and grades; misguided attempts to adapt and combine them are an all too frequent factor in accidents. For example, tying knots in rope causes stress and chains should only ever be joined with purpose-designed components. Furthermore, equipment designed for lashing is rarely suitable for lifting.
More permanent modifications to equipment are another potential cause of accidents and should only ever be performed with the approval and guidance of an appropriately qualified person. The risks are clearly illustrated in an incident that was the subject of a recent court case in London. A young man at his first day of work as a stevedore at a harbour was killed by the jaws of a clam-shaped grab used for moving large quantities of slag and aggregate. The grab, which weighed about two tonnes and closed in a couple of seconds, had been modified a matter of weeks before the accident. Hooks were welded to the inside of the grab, so that the same attachment could be used for moving bags as well as aggregates. However, the modified equipment required staff to work inside the jaws of the grab. The man was killed when the lever that activated the grab was caught in the clothing of the machine operator, causing it to close without warning.
In addition to ill-advised modification and cannibalisation, other common mistakes include the use of equipment that does not allow the hook to be positioned over the load's centre of gravity, or equipment that is too fast to allow the load to be properly controlled. Another warning sign of potential danger is a lifting operation that imposes unacceptable restrictions on the equipment chosen for the job.
Those responsible for lifting operations are faced with an ever-increasing array of equipment that can potentially be employed. Furthermore, legislation designed to encourage safer manual handling has also increased the extent to which lifting equipment is used throughout industry. At the same time, competitive pressures inevitably force the issue of price higher up the agenda. However, whatever the nature of the operation, if a number of basic principles are adhered to, the chances of using faulty or inappropriate equipment will be kept to an absolute minimum. It is essential to use only credible suppliers and look beyond the simple issue of price. Certification, inspection, examination and maintenance procedures should also be rigorously adhered to. Finally, a thorough assessment of the lifting operation must always be undertaken, to ensure that the right equipment is selected for the job in hand.